ACH580 Parameters
Applicability:
The manual applies to the ACH580 HVAC control program (version 2.12). To check the firmware version of the control program in use, see system information (select Menu > System info > Drive) or parameter 07.05 Firmware version on the control panel. For ACH580-31 and ACH580-34, to check the ISU firmware version in use, select Menu > Options > Select drive > QCON-21 and then select Menu > System info >
Drive, or see parameters 07.106 LSU loading package name and 07.107 LSU loading package version on the control panel.
Safety instruction:
Follow all safety instructions.
- Read the complete safety instructions in the Hardware manual of the drive before you install, commission, or use the drive.
- Read the firmware function-specific warnings and notes before changing parameter values. These warnings and notes are included in the parameter descriptions.
Terms and Abbreviations
ACS-x-AP-x=Assistant control panel, advanced operator keypad for communication with the drive. The ACH580 supports the Hand-Off-Auto control panels ACH-AP-H and ACH-AP-W (with a Bluetooth interface).
AI=Analog input; interface for analog input signals
AO=Analog output; interface for analog output signals.
BACnet™=BACnet™ is a registered trademark of American Society of Heating, Refrigerating and Air-Conditioning Engineers (ASHRAE).
BAS= Building automation system
BMS=Building management system
Break Chopper= Conducts the surplus energy from the intermediate circuit of the drive to the brake resistor when necessary. The chopper operates when the DC link voltage exceeds a certain maximum limit. The voltage rise is typically caused by deceleration (braking) of a high inertia motor.
Break Resistor= Dissipates the drive surplus braking energy conducted by the brake chopper to heat. Essential part of the brake circuit. See chapter Brake chopper in the Hardware manual of the drive.
Control Board= Circuit board in which the control program runs.
CCA-01=Cold configuration adapter
CDPI-01=Communication adapter module
CHDI-01=Optional 115/230 V digital input extension module
CMOD-01= Optional multifunction extension module (external 24 V AC/DC and digital I/O extension
CMOD-02=Optional multifunction extension module (external 24 V AC/DC and isolated PTC interface)
CPTC-02= Optional multifunction extension module (external 24 V and ATEX certified PTC interface)
CRC= Cyclic redundancy check. The IPC checks the parameter group validity in terms of CRC.
DC Link= DC circuit between rectifier and inverter.
DC Link Capacitors=Energy storage which stabilizes the intermediate circuit DC voltages.
DDCS=Distributed drives communication system; a protocol used in communication between ABB drive equipment, used for ACH580-31 and ACH580-34 drives.
DI=Digital input; interface for digital input signals
DO=Digital output; interface for digital output signals.
DPMP-01=Mounting platform for ACx-AP control panel (flange mounting)
DPMP-02/03=Mounting platform for ACx-AP control panel (surface mounting)
Drive=Frequency converter for controlling AC motors
EFB=Embedded fieldbus
FBA=Fieldbus adapter
FBIP-21= Optional BACnet/IP adapter module
FCAN-01 =Optional CANopen adapter module
FCNA-01= ControlNet adapter module
FDNA-01 =Optional DeviceNet adapter module
FECA-01= Optional EtherCAT adapter module
FEIP-21= Optional Ethernet/IP adapter module
FENA-21= Optional Ethernet adapter module for EtherNet/IP, Modbus TCP and PROFINET IO protocols
FEPL-02= Optional Ethernet POWERLINK adapter module
FLON-01= LONWORKS® adapter module
FMBA-01= Optional Modbus RTU adapter module
FMBT-21= Optional Modbus/TCP adapter module
FPBA-01= Optional PROFIBUS DP adapter module
FPNO-21= Optional PROFINET adapter module
Frame (size)= Refers to drive physical size, for example, R1 and R2. The type
designation label attached to the drive shows the frame of the drive, see
chapter Operation principle and hardware description, section Type
designation label in the Hardware manual of the drive.
FSCA-01= Optional RSA-485 adapter module
FW Part 1= ACH580 standard control program firmware manual, Part 1 (3AXD50000209811 [English]). This printed manual includes all chapters except Parameters and Additional parameter data. The abbreviation is used in FW Part 2 to refer to items in FW Part 1.
FW Part 2= ACH580 standard control program firmware manual, Part 2 Parameters (3AXD50000209828 [English]). This printed manual includes chapters Parameters and Additional parameter data. The abbreviation is used in FW Part 1 to refer to items in FW Part 2.
ID run= Motor identification run. During the identification run, the drive will identify the characteristics of the motor for optimum motor control.
IGBT= Insulated gate bipolar transistor
Intermediate circuit= See DC link.
Inverter = Converts direct current and voltage to alternating current and voltage.
I/O= Input/Output
IPC= Intelligent pump control
LONWORKS®= LONWORKS® (local operating network) is a networking platform specifically created to address the needs of control applications.
LSW= Least significant word
NETA-21= Remote monitoring tool
Network control = With fieldbus protocols based on the Common Industrial Protocol (CIPTM), such as DeviceNet and Ethernet/IP, denotes the control of the drive using the Net Ctrl and Net Ref objects of the ODVA AC/DC Drive Profile. For more information, see www.odva.org, and the following
manuals:
- FDNA-01= DeviceNet adapter module user’s manual (3AFE68573360 [English]), and
- FENA-01/-11/-21 Ethernet adapter module user’s manual
(3AUA0000093568 [English]) - FEIP-21 Ethernet/IP adapter module user’s manual (3AXD50000158621 [English]).
Parameter= User-adjustable operation instruction to the drive, or signal measured or calculated by the drive
PFC= Single pump and fan control. One drive controls multiple pumps or fans with motors.
PID controller= Proportional-integral-derivative controller, also known as closed loop controller. Drive speed control is based on PID algorithm.
PLC= Programmable logic controller
PROFIBUS,
PROFIBUS DP,
PROFINET IO =Registered trademarks of PI – PROFIBUS & PROFINET International
PTC= Positive temperature coefficient, thermistor whose resistance is dependent on temperature. R1, R2 … R11 Frame (size)
RO =Relay output; interface for a digital output signal. Implemented with a relay.
Rectifier= Converts alternating current and voltage to direct current and voltage.
SPFC=Soft pump and fan control. One drive controls multiple pumps or fans with motors.
STO= Safe torque off. See chapter The Safe torque off function in the Hardware manual of the drive.
How to start up the drive:
Note: Automatic selection of supply voltage is not supported in ACH580-31 and ACH580-34. You must select the supply voltage manually using parameter 95.01 Supply voltage. Follow the instructions below.
How to start up the drive using the First start assistant on the Hand Off-Auto control panel
Safety:
Do not start-up the drive unless you are a qualified electrician. Read and obey the instructions in chapter Safety instructions at the beginning of the Hardware manual of the drive. Ignoring the instructions can cause physical injury or death, or damage to the equipment.
- Check the installation. See chapter Installation checklist in the Hardware manual of the drive.
- Make sure there is no active start on (DI1 in factory settings, that is, HVAC default). The drive will start up automatically at power-up if the external run command is on and the drive is in the external control mode. Check that the starting of the motor does not cause any danger.
- De-couple the driven machine if
- there is a risk of damage in case of an incorrect direction of rotation, or
- a Normal ID run is required during the drive start-up, when the load torque is higher than 20% or the machinery is not able to withstand the nominal torque transient during the ID run.
Hints on using the assistant control panel
The two commands at the bottom of the display (Options and Menu in the figure on the right),
show the functions of the two softkeys and located below the display. The commands assigned to the softkeys vary depending on the context. Use keys , , and to move the cursor and/or change values depending on the active view. Key shows a context-sensitive help page. For more information, see ACx-AP-x assistant control panels user’s manual (3AUA0000085685 [English]).
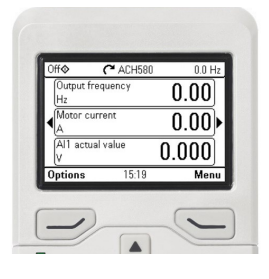
1 – First start assistant guided settings: Language, motor nominal values, and date and time
1.Have the motor name plate data at hand. Power up the drive
2. The First start assistant guides you through the first start-up. The assistant begins automatically. Wait until the control panel enters the view shown on the right. Select the language you want to use by highlighting it (if not already highlighted) and pressing (OK).
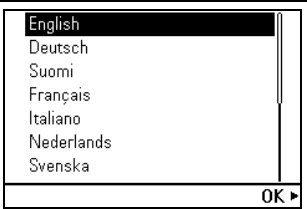
ACH580-31 and ACH580-34 drives: Select the
supply voltage with parameter 95.01 Supply
voltage:
- In the First start assistant menu, select Exit and press (Next).
- In the Home view, press (Menu) to enter the Main menu.
- In the Main menu, go to Parameters > Complete list > 95 HW configuration by selecting the correct row and pressing (Select) repeatedly.
- Select parameter 95.01 Supply voltage and press (Edit).
- Select supply voltage 380…415 V or 440…480 V and press (Save).
- Go back to the Main menu by pressing (Back) repeatedly.
- In the Main menu, select First start assistant and press (Select) to enter the First start assistant menu.
- Continue with the following steps for commissioning the ACH580.
Select Commission the drive and press (Next)
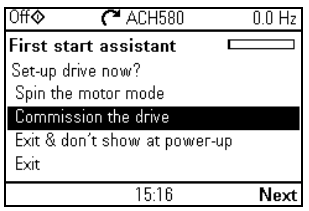
Select the localization you want to use and press (Next)
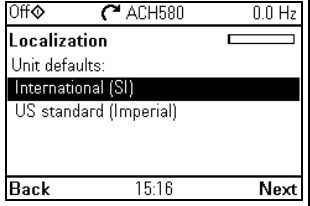
Change the units shown on the control panel if
needed.
- Go to the edit view of a selected row by pressing.
- Scroll the view with and . Go to the next view by pressing (Next).
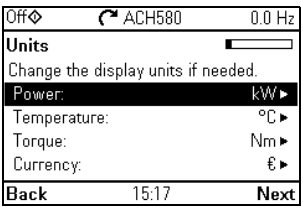
To select a value in an edit view:
- Use and to select the value. Press (Save) to accept the new setting, or press (Cancel) to go back to the previous view without making changes
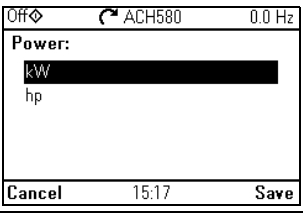
Set the date and time as well as date and time display formats.
- Go to the edit view of a selected row by pressing .
- Scroll the view with and Go to the next view by pressing (Next)
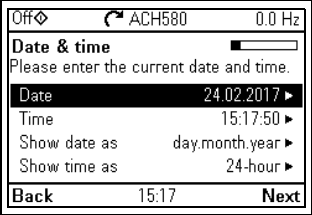
Refer to the motor nameplate for the following nominal value settings of the motor. Enter them values exactly as shown on the motor nameplate. Example of a nameplate of an induction (asynchronous) motor:
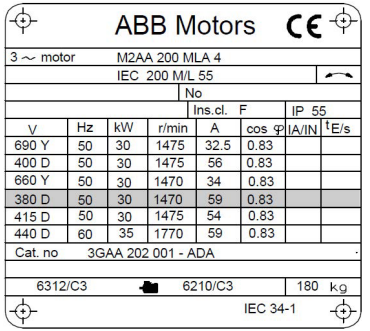