CH-03 ACS5000A Control Units
Welcome to ACS 5000 Service and Commissioning training course, module 5,ACS 5000 Control Unit“.
You will be able to understand and explain to others the structure of the terminal and Control Unit cabinet, the control hardware contained in the Control Unit, such as Printed Circuit Boards, and the auxiliary supply concept of the ACS 5000.
Local Operating Panel:
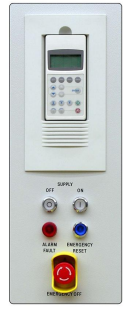
The local operator panel on the door of the Control Unit provides all control functions to operate the drive, for example for testing purposes or if the higher level control system is out of operation. The CDP control panel is a door mounted user interface for local operation. It is the same panel as used on all frequency converters of the ACS family and serves as a basic user interface for monitoring, control and operation of the drive. The CDP control panel communicates with the main control board AMC via a RS-485 interface. Please refer to the User’s Manual for further information about how to use the panel. ON, OFF and EMERGENCY RESET are illuminated buttons. The ON button is for the MCB close request; it will blink during the charging sequence and will illuminate continuously when MCB is closed. The OFF button is for the MCB open request, blinking during the discharging sequence and steady ON when the drive is discharged. The EMERGENCY RESET button is not a
general reset, it is used to reset only the emergency safety relays. Its lamp will blink if an emergency signal is active. The ALARM and FAULT lamp will blink if an alarm is active, and stays steady on if a fault is active. If the EMERGENCY OFF button is pressed during operation, the MCB will be opened and the DC bus will be discharged. The motor stops by coasting. The message “Emergency Off” will be displayed on the control panel
ACS5000A Control Unit:
The Control Unit of the air-cooled ACS 5000 incorporates the hardware for the control, monitoring and
protection functions of the drive and the communication interfaces to the local control panel and to the remote-control devices. Depending on the control concept of the drive system, the remote-control devices include a higher-level control system and / or remote operator stations. The AMC board and Main Interface board are located in the middle of the unit. These are the main components of the drive’s control system and perform drive and motor control tasks. Other internal control devices and the peripheral input and output interfaces to the customer communicate with the AMC board via eight fiber optic DDCS communication channels. The Main Interface board is mounted under the AMC board. They communicate with each other through a 64 way ribbon cable. Through this Main INT board, the control system can communicate with the Phase INT circuit boards inside the power cells. The OEI board used for fast MCB trip is mounted to the right of AMC and Main INT. Below the AMC board is the standard S800 I/O cluster 1. By default, we suppose that the ACS 5000 will be controlled via overriding system, there are no terminals reserved for external control signals and a fieldbus adapter will be delivered together with the drive. If the customer wants to control the ACS 5000 by hardwired connections, an optional S800 I/O cluster 3 will be mounted in the upper part of the cabinet. When you open the swing frame, you get access to the Earth Fault supervision board EAF. Below that, there are the IPS number 7, the high voltage charging relays and the charging transformer.
ACS5000A Terminal Unit:
The Terminal Unit provides the terminals for the feeder and motor cables and the ground bus bars for the
termination of the ground cable and the cable screens. In the air-cooled ACS 5000, the terminal compartment is accessible when the swing frame of the Control Unit has been opened. All power cables, either from transformer secondary side to ACS 5000 or from ACS 5000 to the motor, are located here. The cable entry is prepared in the factory according to the cable entry configuration. Top or bottom cable entry are both possible.
ACS 5000A Control Overview:
Generally, the control hardware of the air cooled ACS 5000 can be divided into two parts: The central
processing unit consisting of the AMC34 board together with the Main INT board, which contains all functions that are common to all three phase units. The external interfaces are communicating via 8 DDCS channels with the AMC board. On the other hand, we have the local boards on each phase unit such as the Phase INT and CVMI boards. They are responsible for the control of the local modulator and for the measurements. The communication between the central Main INT and the local Phase INT boards is done through PPCS links.
ACS5000W Control Unit:
There are two generations of water-cooled ACS 5000. However, the main control devices are the same: The AMC board and Main Interface board, the standard S800 I/O cluster 1, and the optional S800 I/O cluster 3. In the generation 1, the MCB trip control OEI board and the discharging OEI board are mounted on the left side of the COU frame. In the generation 2, the MCB trip control OEI board is mounted on the swing frame, whereas the discharging control OEI is located in the PCU. Each PCU has it’s own OEI board for the discharging circuit.
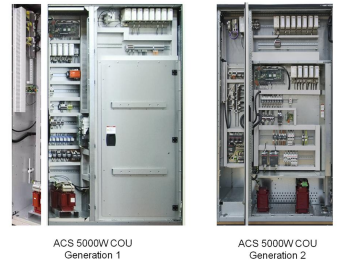
ACS 5000 W Terminal Unit (Generation -01):
In the water-cooled ACS 5000 of the first generation, the transformer cables and the motor cables are
connected to separate cabinets. The first unit of the drive contains the terminals for the transformer cables and the ground cable. The transformer cable screens are also connected there. The motor cables are connected behind the cover plate in the Control Unit. The Earth Fault supervision board EAF, the charging transformer and the high voltage charging relays are also there.
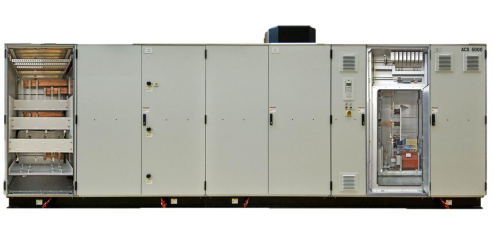
ACS 5000W Terminal Unit (Genration-02)
In the water-cooled ACS 5000 of the second generation, the mechanical structure is a completely new design. There is no individual Terminal Unit anymore for the transformer cables. They are directly connected to the rear side of the phase unit. The motor cables are connected to the bus bars which are behind the swing frame of the Control Unit. The Earth Fault detection board EAF, the charging transformer and the high voltage charging relays are still there.
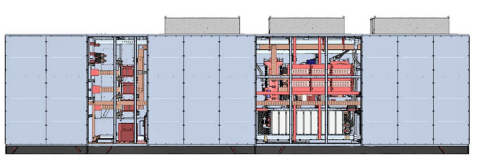
ACS5000W Control Overview:
The water-cooled ACS 5000 has a similar control configuration as the air-cooled version. The functions which are common to all three phase units are handled by the AMC and Main Interface boards. The Phase Interface boards are responsible for the local modulator in each phase. But there are three obvious differences between air cooled and water-cooled drives. First, the S800 I/O cluster 2 is used for the Water-Cooling Unit control. This cluster does not exist in air cooled drives. Secondly, the water-cooled ACS 5000 has discharging circuits which need to be controlled. In generation 1, the discharging signal is coming from the Main Interface board, and all three DC links are discharged at the same time via an OEI board. In generation 2, each PCU has it’s own.
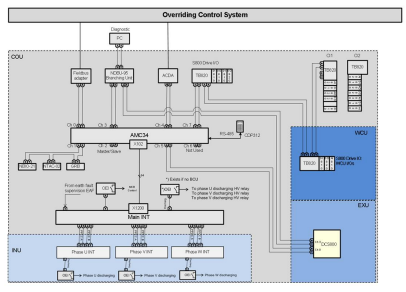
AMC 34 Board:
The AMC board is the main control board of the drive. It handles most of the motor and inverter control
functions. The software protections are also implemented in the AMC board. The only hardwired communication link of the AMC board is the RS-485 interface to the CDP control panel. All other communication channels are fiber optic. Eight DDCS channels ensure the communication with the field such as overriding system, I/O’s and encoders. The two PPCS channels are not used in ACS 5000. The communication to the Main Interface board is done by a 64 way ribbon cable connected at X102. The Flash PROM is a permanent, programmable memory. It contains the firmware and the actual project specific parameters. Another Flash PROM is used for the black-box function. The other components on the board are: The Digital Signal Processor DSP; the Application Specific Integrated Circuit; and the fast static RAM, a volatile memory which is always re-loaded when the board is powered up. Under the firmware Flash, there is the Booting PROM, managing the transfer of the program from the Flash PROM to the fast static RAM during the initializing sequence. The AMC board has ten status LED’s. The LED’s relevant for ACS 5000 are: P, green, means Power Supply OK; T1, yellow, will be on when there is traffic on the communication channel 0; T2, also yellow, will be on when channel 3 is used. Two LED’s, F red, and M, green, will be on during the booting sequence, when the AMC board is powered up.
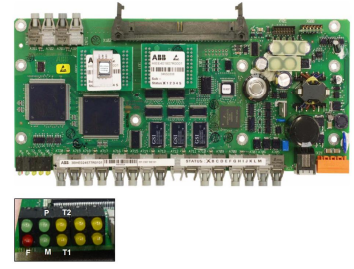
AMC Board Flash PROM:
The Flash PROM is programmable via channel 3 of AMC board, either by downloading a back-up package with one of the software tools, or by downloading a firmware version under DOS. When loading a new firmware version into the Flash PROM, attention must be paid to the compatibility between the software version on the Flash PROM and the software versions on the other control boards in the drive. The Flash PROM is installed on a socket; it can be easily replaced, if necessary, but the socket does not have a positioning key. The operation requires attention. Besides the ESD protection measures, the position of the white dot on the AMC board must match the position of the not-so-visible dot on the Flash PROM sub-board. There is not a second chance if the Flash PROM is misplaced, and the AMC board is powered up. The booting PROM located under the Flash PROM is visible in this slide.
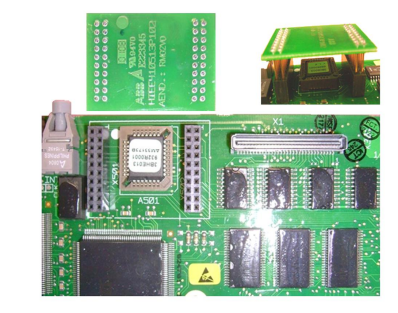
AMC 34 CH00: Field Bus
The AMC board DDCS channel zero is connected to the Fieldbus Adapter. The Field Bus Adapter, FBA, is an interface used for the serial, bidirectional communication between the AMC board and the upper-level control system, if the controller does not use the ABB DDCS or Drive Bus protocol. Through the fieldbus interface, the converter can be controlled, and status messages, reference and actual values can be transmitted. A wide range of Field Bus Adapters is available, depending on the type of PLC used by the application. The most common types are Profibus adapters, generally for Siemens PLC’s, but not only, AF100 adapter for ABB Advant controllers, Modbus adapter and Ethernet adapter.
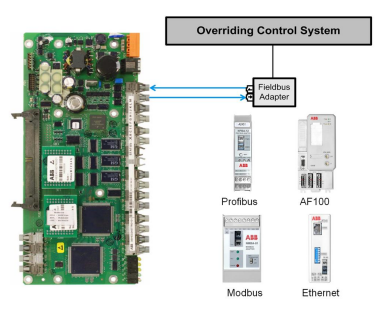
AMC 34 CH01: Option Module:
The speed encoder, position encoder and fast I/O module NBIO21 could be connected to channel 1 as an
option, and all of them are connected in a ring topology. In this situation, each module or encoder will have a specific address.
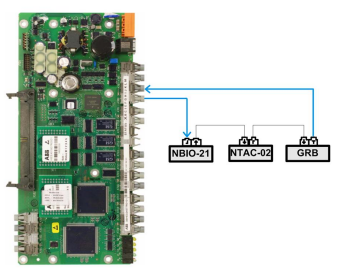
AMC-34 CH02: Master Follower Control Option
The Master/Follower function is designed for applications, in which the system is run by several ACS 5000
drives and the motor shafts are coupled to each other via a mechanical system. The external control signals are connected to the Master ACS 5000 only. The Master controls the Follower via the fiber optic serial communication channel 2. Maximum 4 Follower drives could be connected to one Master drive via a ring connection. You can find more details in the Signal and Parameter Table. Parameter group 41 is used for this function.
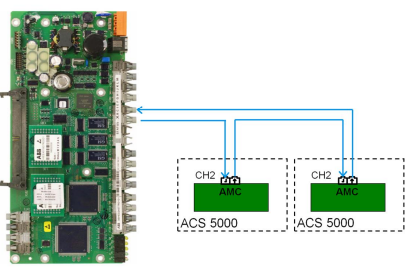
AMC 34 CH3: Drive window Drive Monitor:
Channel 3 is used to connect a computer provided with software tools, either Drive Window, Drive Debug or Drive Monitor.
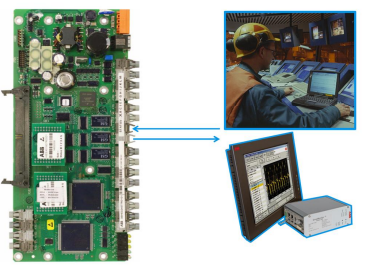
AMC 34 CH04: Synchronous Bypass Option:
Channel 4 is used for the synchronous bypass function. This is an option for the converter to control the transfer of one or several motors to a fixed frequency line and back to the converter with only a very short power interruption.
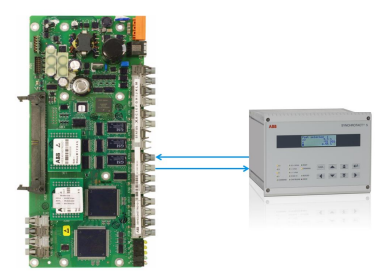
AMC-34 CH05: Excitation Unit (synchronous motor):
For synchronous motor applications, an Excitation Unit is required. The control and status communication
between the AMC board and the control board of the Excitation Unit is done through channel 5

AMC-34 CH0 7 :S800 I/O Module:
Channel 7 is connected to the S800 I/O clusters via the bus modem TB820. For standard I/O’s, internal signals are connected to the I/O modules directly. The external signals are connected to terminals inside the Control Unit and are then internally wired to their I/O modules. For optional I/O’s, the external control signals have to be connected directly to the S800 module terminals.
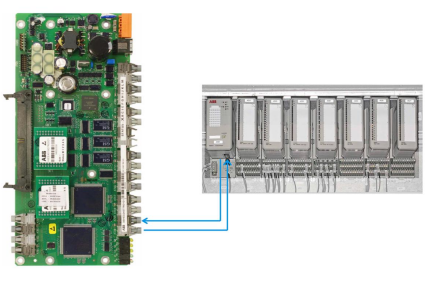
Pulse Encoder Adapter NTAC-02 (option)
The pulse encoder adapter is an interface for an incremental encoder, used for speed measurement in
applications requiring very accurate and fast speed control. The pulse encoder is hardwired at the terminal X1. The adapter has a DDCS channel connected to channel 1 of the AMC board. The pulse encoder has two outputs channels with 90° phase shift between them. The frequency of the pulses gives information about the speed, and the phase shift gives information about the direction of rotation. For most of the encoders, when turning forward, or clockwise, channel 1 is leading, and when turning reverse, channel 1 is lagging. As the position encoder cables, the pulse encoder cables must be also twisted pairs, individually shielded and with an overall shield
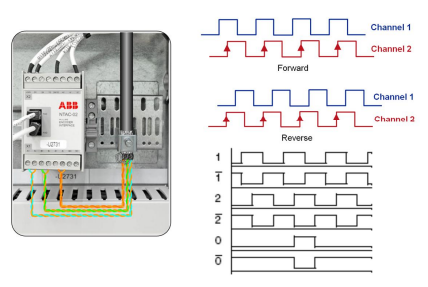
Grey Encoder Adapter LD GRB-01:
In applications with synchronous motor, the relative position of the rotor must be known at any time. To detect the position of the rotor, a 13-bit Gray coded absolute encoder is used. The Gray code is used in order to eliminate any risk of hazard in the transmission of the position of the rotor. Unlike the standard binary code, the gray code changes only one bit at a time. The Gray encoder adapter used in ACS 5000 is LD GDR-01. It communicates with the encoder by the mean of a terminal board installed in a terminal box on the synchronous motor. The communication with the AMC board is done over an optical DDCS interface connected to channel 1 of AMC board. The position encoder cables must be twisted pairs, individually shielded and with an overall shield

Fast I/O Module NBIO-21:
The NBIO-21 fast I/O module contains two fast analog inputs. This allows a fast modification of the speed
and/or torque reference value via external analog signals. The function can be disabled or activated
independently by parameter. The function is implemented on the 2 ms time level.
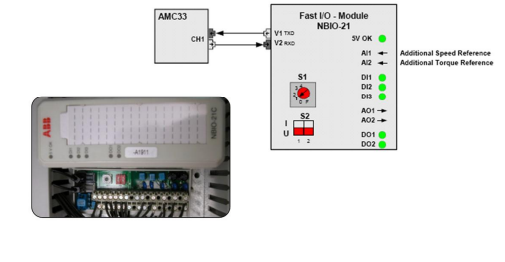
S800 I/O System:
The hardwired field and drive related I/O’s are connected to ACS 5000 via the standard ABB S800 system.
S800 is a distributed modular I/O system used with ABB Advant controllers, such as AC80 or AC800. The AMC software platform is able to communicate directly with the S800 I/O system via fiber optic channel 7. The main components of this system are the following: TB820 Bus Modem. It is a fiber optic interface between AMC board and the actual I/O modules, connected to the I/O modules by way of an electrical bus and Module Termination Units. X5 will be connected to channel 7 of AMC board. The second fiber optic channel of TB820, X4, is connected to the next cluster. The Bus Modem has a rotary switch for the address setting. Six LED’s provide information about the status of the Bus Modem: F, red, Fault; R, green, Running; P, green, Power supply OK; Rx1 and Rx2: fiber optic channels receiving data; ERx: electrical bus receiving data. MTU, the Module Termination Units, are passive units distributing the electrical bus to the actual I/O module installed on it and to the next Module Termination Unit. The last MTU in the cluster has a small Bus Terminator, TB807, plugged into the electrical bus connector. Two mechanical keys are used for the identification of different types of modules. The I/O module is locked in the Module Termination Unit by a locking tab. When in position “unlocked”, as it is shown in this picture, the locking tab will also disable the module. Consequently, the I/O module can be removed from the Termination Unit without disconnecting the control power. The actual I/O modules have yellow LED’s for the status of the I/O’s and three LED’s for the status of the module: Fault, Running and Warning. Different types of I/O modules have different fixed coding keys. Before the I/O module is inserted, the adjustable mechanical keys on the MTU must be adjusted to match the code

ACS5000W S800 I/O Configuration:
The standard interface package is always part of the drive. The air-cooled ACS 5000 has the cluster 1, located in the Control Unit, as the standard I/O interface. The TB820 terminal X5 is connected to channel 7 of AMC via fiber optics. All the I/O signals related to the drive, the MCB and the cooling fan control are connected here. The standard air-cooled ACS 5000 was designed to be controlled by the overriding system, so there is no interface for external, hardwired control signals. To control the ACS 5000 through hardwired signals, two types of interface extension could be used. All the functions of the terminals are predefined in the software, so the cables need to be connected to the specific terminals according to the electrical drawings. The optional modules need to be enabled in the parameter group 75.
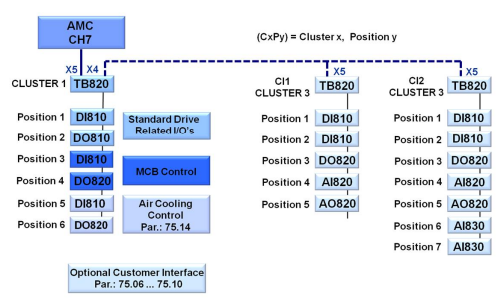
For the water-cooled ACS 5000, the cooling fan control related I/Os are not necessary anymore. Instead, an extra cluster 2 located in the Water-Cooling Unit will be used for the control and supervision of the water-cooling system
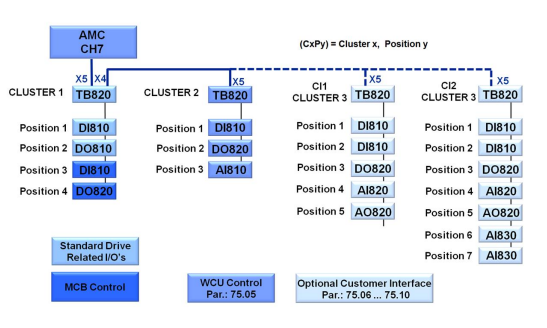
Main Interface Board (INT2)
The Main Interface board is the same INT2 board as the Phase Interface boards, but the installed software is different. The software version must be compatible with the type of the unit and with the software versions installed in other boards in ACS 5000. It can be downloaded to the Interface board using the appropriate tool. The software downloading package can be found on the ABB MV Drives Portal. The Main Interface board is used for fast hardware protections, PPCS communication and other functions that are common to all three phase units. It is connected directly to the AMC34 board via a 64-way ribbon cable. Fiber optic cables are used for data transmission. Totally, it has 26 optical transmitters and 21 receivers. Nine LED’s are used to indicate the status of the Main Interface board. LED 1 is on when the PPCS link between Main INT and Phase INT’s is enabled. LED 2 is on when a fault is pending. LED 3 is on when the power supply is OK. LED 6 is on when the system did a firing through. The LED named Done is used for FPGA configuration indication. All other LED’s are not used in our case.

ACS5000A Main Interface Connection:
Here are the devices shown, which are connected to the air-cooled ACS 5000 Main Interface board. Three
Phase Interface boards are connected via PPCS links. The Earth Fault supervision board EAF feedback signal is also connected to the Main INT. In case of a severe fault, such as short circuit, the drive needs to perform a firing through which requires a fast opening of the MCB. This MCB trip signal will be generated by the Main Interface board and sent to MCB control via OEI board.
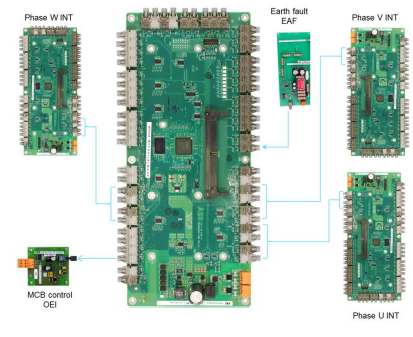
MCB Control OEI:
The OEI, or Optical Electrical Interrupter, is a small electronic board used to trip the MCB as fast as possible in case of critical faults. It is connected to a fiber optic transmitter of the Main INT board, and it has an electronic relay wired to the coils of the MCB relays. As long as the OEI receives a light signal from the Main INT board, the MCB is controlled by the AMC board via digital outputs. If the OEI loses the fiber optic signal from the Main INT, it will immediately trip all the relays involved in MCB control, causing the instantaneous opening of MCB. The reason to let the Main INT board trip the MCB is in the measuring and protection chain. Because the most important drive parameters, like DC bus voltage and AC currents, are acknowledged first by the INT board. In case of a critical fault, the Interface board has the possibility to trip the MCB faster, before the information reaches the AMC board.
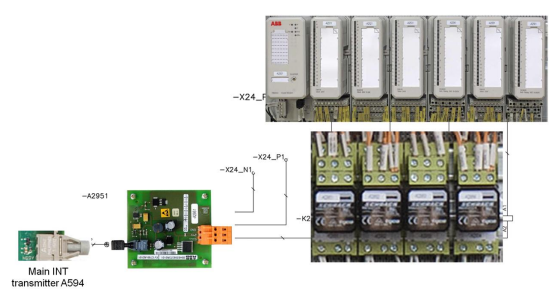
ACS5000W (Gen-01) Main Interface connection:
The water-cooled ACS 5000 of the first generation has the similar connections as the air-cooled ACS 5000. Except that, one more OEI board is connected to the Main INT (A593) for DC link discharging control.
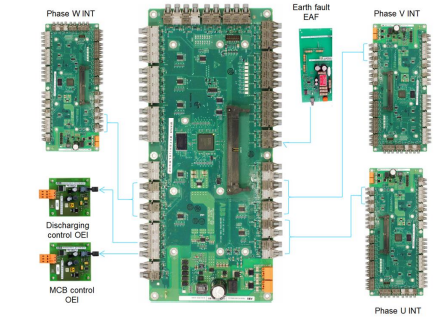
Discharging control OEI:
In the water-cooled ACS 5000 of generation 1, an OEI board is used to discharge the three DC links at the
same time. The discharging sequence is started with a fiber optic signal from the Main INT board in COU. The OEI board converts the signal to an electric signal, which is used to control all three high voltage discharging relays in parallel at the same time.
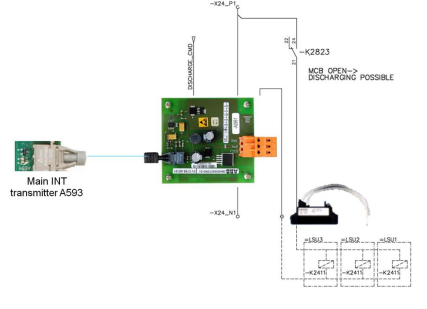
Charging control of OEI:
Unlike other types of ACS 5000, the new generation 2 water cooled ACS 5000 controls the charging transformer secondary side high voltage relays by an OEI board. After the charging order was generated, the S800 Digital Output will close the primary low voltage relay. Then, the main INT board will send a low active signal to the OEI board of the charging control to close the three high voltage relays.
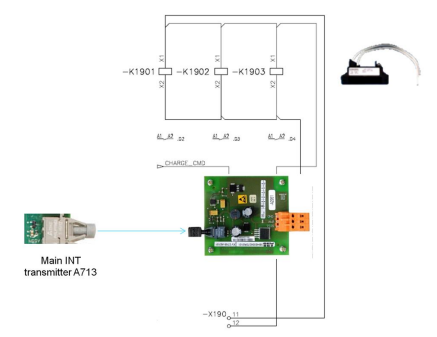
ACS5000 Auxiliary Power Supply:
The total auxiliary power demand of the ACS 5000 includes the auxiliary power for the cooling system, the
charging unit and the power for the control hardware and the gate units. The desired voltage level for the auxiliary power needs to be specified when ordering the drive. The auxiliary power for the cooling fans, the cooling pumps and the charging unit is supplied to the drive by a three-phase AC power supply (380VAC -480VAC) and the control power by an Uninterruptible Power Supply to a separate single-phase AC or DC input. (110VDC or 230 VAC) Feeding the control power separately by an UPS has the advantage that the main control hardware will remain energized, the full ride-through capabilities of the drive can be used and the communication to a higher-level control system will not be lost in the event of an auxiliary power outage. Optionally, the total auxiliary power can be supplied to the drive by a three-phase AC power supply. If the power supply is interrupted, drive internal capacitors provide a backup for the control hardware between 0.5 and 3 seconds. The backup enables the drive to ride-through or to perform a controlled shutdown. Additionally, separate power supplies might be needed for other options like converter space heaters, an Excitation Unit or a Synchronized Bypass Unit.
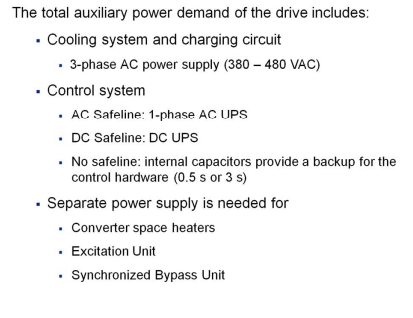