CH-00 ACS 5000A Pre Overview
Items covered by delivery
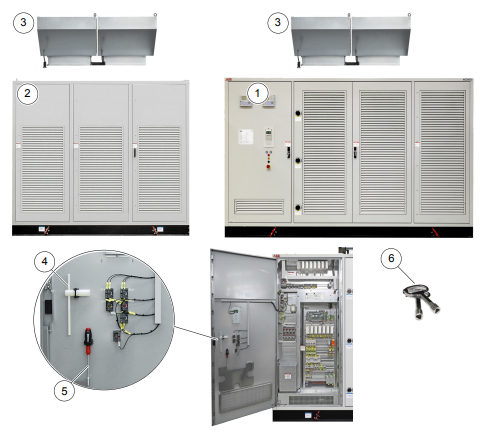
Drive (1) and transformer (2): The transformer is either an integrated or a nonintegrated type.
The cabinets are either shipped in sea freight or airfreight packaging. Fans (3): The fans are shipped in a separate container. The number of fans depends on the cooling configuration ordered. Grounding switch lever (4), Triangular nut driver (5), Door keys (6)
Important Note on Main Circuit Breaker:
The main circuit breaker (MCB) is the drive’s primary protection device. If there is a serious fault with the drive, the MCB must immediately disconnect the drive’s main power supply. To avoid a hazard to personnel and further damage to the equipment, the main power supply must be disconnected immediately upon receiving an open or trip command from the drive. The MCB is located on the primary side of the input transformer.
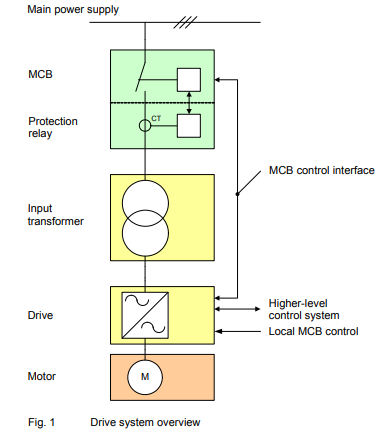
Figure depicts a single-line diagram of a typical drive system, including the main power supply, MCB, input transformer, drive, and electric motor. The MCB is a switching device that disconnects the power supply when necessary or during a fault. Typical devices for MCBs are
- Vaccuum Circuit Breaker
- SF6 Circuit Breaker
- Fused Contactors or motor control centers.
A dedicated protection relay is used for
- Transformer primary cable protection
- Transformer Protection
- Transformer secondary cable protection
- Backing up the drive protection.
In general, these protective measurements are not included in the drive as provided by ABB.
Safety and Protection Requirements:
To ensure safety and protection, the MCB must meet ABB MV Drives’ minimum requirements. It is the system integrator’s responsibility to ensure that all minimum requirements are met. This note and ABB’s medium voltage drive specifications outline the minimum MCB requirements for each drive type. The drive’s safety requirements align with the following standards.
■ ISO 13849-1 Safety of machinery – Safety-related parts of control
systems – Part 1: General principles for design, section 6.2.6 Category 3
■ IEC 60204-1 Safety of machinery – Electrical equipment of machines
- Part 1: General requirement
Minimum Requirements of MCB and MCB control
■ Wire the MCB open/trip command directly from the drive to the MCB. The trip command cannot be wired through a PLC or DCS system unless it meets SIL 3 level requirements and the timing requirements listed below. The drive must be able to open the MCB at any time. Interrupting the open or trip command, such as with a local-remote switch in the MCB, is not permitted.
■ When the MCB is in service mode, only the drive can close it. Local closure of the MCB is not permitted.
■ The maximum opening time of the MCB should not exceed the product or project-specific maximum time specified in the specifications. Typical maximum drive values are defined as follows:
■ Maximum protection trip time is 75 ms.
The maximum protection trip time limits the breaking time (open and arcing) of the device after the open command to prevent further damage to the drive, such as diode failures.
■ Maximum safety trip time is 500 ms.
The maximum safety trip time allows for safe disconnection of the main power supply, preventing any potential hazards to personnel.
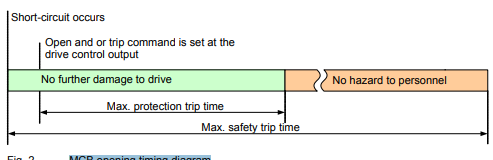
MCB Opening Timing Diagram
To meet safety requirements, it’s recommended that:
The MCB may have two independent opening coils, one opening coil and an undervoltage coil to monitor the control voltage, or an upstream protection coordination scheme that uses the “breaker failure” (ANSI 50BF) signal to automatically trip the upstream breaker if the MCB does not open. Following a failure, the upstream breaker must open within the maximum safety trip time.
Maintenance Recommendation:
The MCB trip circuits should be checked once yearly.